Ann Arbor-Based FordLabs Is Ford's Ongoing Push To Make Automotive Agile
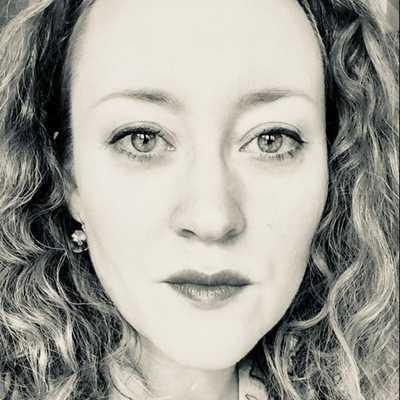
By Laura Cowan
Laura K. Cowan is a tech, business, and wellness journalist and fantasy author whose work has focused on promoting sustainability initiatives and helping individuals find a sense of connection with the natural world.
Abbey Knick, FordLabs Operations & Communications Manager, stands with Office Director John Handy in the open workspace of FordLabs in Ann Arbor.
There was one moment that convinced us Ann Arbor was going to make it through the birth canal as a growing tech hub, and that was when Ford decided to locate a new agile software consultancy, FordLabs, in Ann Arbor, to recruit University of Michigan software development talent to help make the 100-year-old automaker more agile and lean. Where Ann Arbor's arts and tech culture meet the automotive giants of Detroit, FordLabs sits at the crossroads, not just of shifting best practices but of time. John Handy, Office Director of FordLabs who welcomed us in with several other key players in the organization for a tour, told us this is really nothing new. People forget, ourselves included, that lean startup culture was in part born here in Detroit, in lean manufacturing.
“It's been fun to watch," Handy says. "What you’re seeing with agile and lean manufacturing: those have deep roots in Southeast Michigan. A lot of people who signed the agile manifesto worked at Chrysler in the Eighties. That left and went to the coasts and then came back. A lot of it came from Toyota and Chrysler. The same thing came on the lean side. That came from Toyota and Motorola. It went out to the coasts again, where folks said hey these same lean concepts apply to digital products not just assembly lines. It started here, went out, now it’s coming back. It makes sense becasue the industrial backbone of the world came from this region. It feels like a tech renaissance is going on here.”
Mike Rays, FordLabs Product Management Lead, took us around the office and showed us the space where FordLabs works to immerse Ford teams in agile, lean culture, to work alongside them in a human-centered design process to develop custom software projects for Ford. “We opened up a partnership with Pivotal," Rays explains of FordLabs introduction to the Ann Arbor tech scene. "At the end of 2018 Pivotal vacated their presence here, and we had to stand on our own. It was nice having them as a partner," Rays says, in order to get started in Ann Arbor.
"The main reason we moved into Ann Arbor was to tap into the talent," Rays tells us, "and it comes with some other luxuries like being in an urban area. It’s definitely lived up to the hype. We have a lot of people who otherwise would not have joined Ford. Ultimately we will have this [location] and then the train station in Detroit.”
We ask the team if other automakers are following suit. It seems Toyota, Hyundai, and Honda locate engineering, research, and development facilities in Ann Arbor, but don't have the same agile setup as Ford.
Handy explains: “Other OEMs have stuff in the area but we’re all using it differently. Honda is doing something where they rely on the community in places to crowdsource some ideas.”
Rays: “Ford does that too with City Solutions Group. They go in and create a challenge with community members to submit proposals.”
Rays takes us around the space. The central area used to be walled off. It’s multi-purpose now, used as a lunchroom and a location for daily standups and lunch and learns. "It’s a pretty pure form of lean startup human centered design extreme programming here,” Rays says.
The lunch and learn area, left, is where FordLabs employees and visitors host standup meetings and work together in an immersive lean startup, human-centered design culture.
Any twists? “It’s pretty important for us to stay pure because we need to differentiate ourselves from the big IT agile effort that’s happening in Dearborn," Rays explains. "We’ve learned how to navigate internal processes and systems.”
We have spoken before with consultants who are called in to Ford from the outside, to make it easier for teams to adopt external input on best practices. Rays says that's one of the reasons having FordLabs in Ann Arbor works. “We’re treated sort of like a consultancy. We have that drive to make Ford better, and we’re in it for the long haul, but people look at us like we’re different than what we’ve traditionally looked at as software development.”
Challenges in getting agile adopted in a hierarchical corporate culture: “If you think of the 3 big disciplines we have in lean startup culture, human centered design and extreme programming, we don’t have to teach people why being customer centric is important," Rays says. "The company at the highest levels is pushing that…. Paired programming and short iterations with continuous deployment is foreign language to a lot of people, and we built up enough of a rapport that software is enterprise grade, it works, people don’t really question that stuff. The harder part we have to get people over is the lean startup culture, because the business is used to saying, 'This is what we need to build. I’m either going internal or externally to get it built.' We say, 'How do we know that’s what we need to build and that will solve the problems with our customers?' We found a niche inside the organization. People are receptive to it. Groups come to us and say, 'We’ve heard FordLabs is great,' but it’s just new to them. Introducing agile is a whole different group called the Transformation Office whose job is to make the organization more agile by saying we do standups, we do retrospectives, iteration planning, our teams are balanced with software engineers and product planners and designers.”
Ford is pushing this effort across the whole organization, though it’s still slow. Rays says Ford has been attempting to make Ford more agile for the last 12-15 years, which is not quick by any means. Still, it takes time to shift culture and practices in an organization so large and a culture with so much deep heritage that requires multiple layers of management and integration and safety regulation. “We’re 70 people, we can only influence so much at a time. We use our software development and the teams we’re working with to spread the way we work. We see it as a mission to make the company more lean.”
Main Street conference room at FordLabs has a garage door that opens to the main area of the office, for more open parties and meetings. It fits nicely with the mobility theme, and the door is overlaid with a map of Ann Arbor's roads. You are HERE, in the heart of things, right down town with about 250 other tech companies.
Abbey Knick, Operations & Communications Manager, introduces us to some of the team. A group take a break to play video games while the rest of the office huddles in small groups on projects and in meetings. “Pivotal gave us some of the tools to stand on our own," Knick says. "We weren’t just sharing the space. We were working actively on projects and engagements.” She shows us how the team is organized in space, so that they can communicate well at close quarters for quick turnaround on projects.
“We keep the standup, the regular pingpong break, some of the ways we run retrospectives and those practices we kept from Pivotal," Knick says. "A few things we got rid of because it wasn’t working with the way we work with other groups. We also do lunch and learns together.”
“We have 2 or 3 teams stationed at the factory working on projects. Sometimes we’ll get people in Dearborn and vice versa. When we’re working with a team we ask people to spend time co-locating with us, to better understand our practices and a way to foster communication and context. I think that is a Pivotal practice to work so closely with all members of the team.”
Main Street is the largest conference room, overlaid with a map of Ann Arbor’s streets marked with FordLab’s office location. Teams across the Ann Arbor-Dearborn divide are laid out on boards, to show people in real-time who is working on which project--to make the team structure visible.
One of the major reasons automotive needed to go agile was to keep up with integrating quickly changing tech into rather long multi-year vehicle product development cycles. How does Ford keep up with an accelerating product and design cycle as the feedback and technology development loop keeps getting shorter and shorter? Knick says Ford handles this by layering projects into different lengths: “We spend time scoping and qualifying a project to see what they’re looking for and what their business outcomes are. We set the expectation at the beginning that we will get to work with users from the start of the project, that we will be able to be delivering quickly. There are other groups in Ford that work a couple years out mindset, and there are groups at Ford that work on longstanding projects. We often work on new ideas and have the opportunity to validate them. The group that came in with the idea has the resources to take it back and dedicate a team. Some things we have are still longstanding and we have different lengths of engagements. We’ve had projects that have stayed over a year and ones that have been under 3 months. The expectation is that we work at the beginning of the process."
John Handy: “The company has a series of tools they’re employing right now to agile-ify Ford. One is the Transformation Office, whose whole job is organizational change management deploying coaches throughout the organization to help grow them. FordLabs is another one of the tools in the toolbelt, but we use a very different approach to solving the same problem. We partner with marketing or manufacturing or mobility and we will build a product alongside them, and throughout our engagement we’ll start transferring ownership of what we’re working on back to them so that allows us to have a wide reach. At any given point, half of our portfolio of 12 [concurrent projects] are doing exactly that. Right now a specific example is Oculus, which is building a tool in partnership with Ford’s Analytics division to help Ford decide what features to put in the upcoming vehicle lines that are deeper in the cycle plan. It’s reporting, it’s data analysis, but when we did this we partnered with the whole organization, and they’re now supplying their own engineers, their own product managers, their own designers, and then we work alongside them to teach them our practices.”
FordLabs, upper left, is located inside the Llamasoft building on Division in downtown Ann Arbor.
“We will do some basic assessments to make sure folks are going to be receptive and have the right mindset to the practices we’re going to give them," Handy says. "Baked into the model is teaching through demonstration. It’s not classroom, it’s working alongside you. We always try to be the big bucket of black paint and they’re the little red drops. In everything we do from enablement or uplift perspective is we try to be overwhelming numbers. That’s one of the reasons we’re in Ann Arbor. We bring small groups in and overwhelm them with culture. For an individual product, we bring in people we’re working with in small numbers in a reverse coaching model. We use a very different approach to do organizational change.”
Handy says it's not about teaching people what to do either. It's about bringing them alongside in the process and showing them how the process functions in real-time. What he is describing is the same immersive model that is considered ideal for a wellness retreat, or the building of community on a farm. In fact, the same day we interviewed Handy and the FordLabs team, 2 other people in these diverse fields explained the same process in their own industry as the one key to creating community, influence culture, and create lasting change in an organization or individual looking to build new habits. This is no accident. Lean startup culture taps into an aspect of human psychology that makes all of these processes work. But change and adoption take time.
“Over the course of the year we work on 30 things, so that’s 30 times the number of people we’re working with whose lives we touch," Handy says. "I don’t think we cast as wide of a shadow but it’s deep. Folks are going to spend time at FordLabs and as they go into the rest of the organization, they’ve got a heavy megadose of our practices.”
“Ford is really recognizing that software and technology aren’t just support organizations for automotive anymore. The company is making large investments into software and there is a recognition that software is core. As new categories and industries have emerged within automotive such as mobility and autonomy it feels like there has been a renaissance of tech coming from the automotive sector.”
abbey knick, agile automotive, agile mobility software, automotive news, automotive software, extreme programming, ford, fordlabs, human centered design, john handy, lean startup, mike reys, mobility tech